
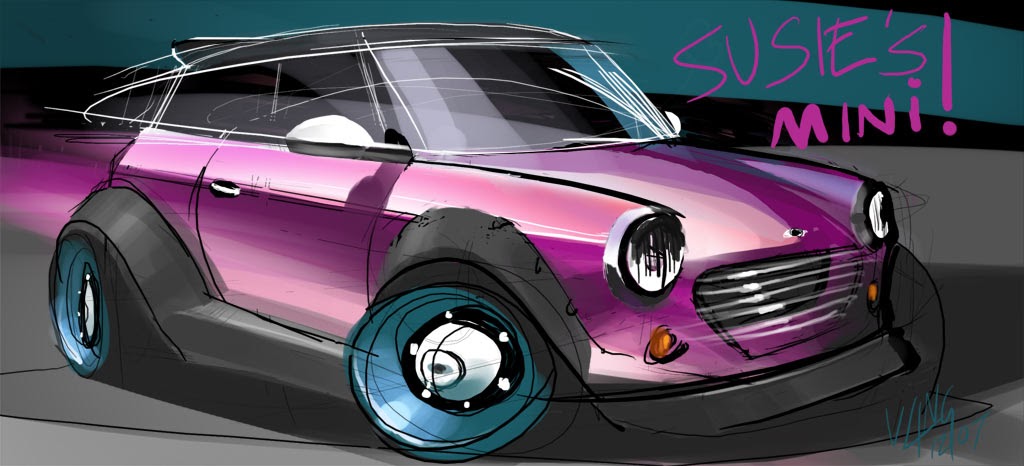
It cuts costs by getting rid of production lines.

The additive approach to manufacturing has several big advantages over the conventional one. A basic 3D printer, also known as a fabricator or “fabber”, now costs less than a laser printer did in 1985. But like computing before it, 3D printing is spreading fast as the technology improves and costs fall. As with computing in the late 1970s, it is currently the preserve of hobbyists and workers in a few academic and industrial niches. Small items can be made by a machine like a desktop printer, in the corner of an office, a shop or even a house big items-bicycle frames, panels for cars, aircraft parts-need a larger machine, and a bit more space.Īt the moment the process is possible only with certain materials (plastics, resins and metals) and with a precision of around a tenth of a millimetre. The beauty of the technology is that it does not need to happen in a factory. Eventually the object in question-a spare part for your car, a lampshade, a violin-pops out. Products are thus built up by progressively adding material, one layer at a time: hence the technology's other name, additive manufacturing. A machine nearby whirrs into life and builds up the object gradually, either by depositing material from a nozzle, or by selectively solidifying a thin layer of plastic or metal dust using tiny drops of glue or a tightly focused beam. First you call up a blueprint on your computer screen and tinker with its shape and colour where necessary. It may have as profound an impact on the world as the coming of the factory did. Three-dimensional printing makes it as cheap to create single items as it is to produce thousands and thus undermines economies of scale. Now a new manufacturing technology has emerged which does the opposite. THE industrial revolution of the late 18th century made possible the mass production of goods, thereby creating economies of scale which changed the economy-and society-in ways that nobody could have imagined at the time.
